Revista
Fuentes: El Reventón Energético
Vol. 15 Nº 1 de
2017 - Ene/Jun - pp 27/40
OPTIMIZACIÓN
DE LA TASA DE
PENETRACIÓN
MEDIANTE EL ANÁLISIS
DE
LAS VIBRACIONES AL PERFORAR, CASO DE ESTUDIO ECUADOR
Diego
Ayala*; Alina Benítez; Raúl Valencia
Facultad
de Ingeniería en Geología y Petróleos. Escuela Politécnica Nacional. PO.Box
17-01-2759. Quito. Ecuador.
*E.mail:
diego.ayala.t@gmail.com
RESUMEN
La exposición a las vibraciones en la construcción de un pozo es un
fenómeno inherente a la perforación, las geometrías cada vez más complejas de
los pozos, así como la dureza de las formaciones atravesadas son algunos de los
factores que propician condiciones desfavorables y potencian un fallo prematuro
de las herramientas de perforación. El estudio expone el proceso de
optimización llevado a cabo para perforar la formación Napo (Cuenca Oriente) en
la sección de 12 ¼”, mediante el uso de sensores de vibración para registrar la
dinámica de perforación; el análisis se realizó en tres pozos, todos ellos con
geometría tipo “J”. La correcta interpretación de los registros y la
implementación de las recomendaciones que dieron como resultado del análisis
pozo a pozo, permitieron realizar cambios en el diseño del BHA y establecer
parámetros de perforación, que resultan en menores niveles de vibración y por
lo tanto en mejores desempeños.
Palabras clave:
Vibraciones al perforar, Optimización de la perforación, Problemas al perforar.
OPTIMIZATION OF RATE OF PENETRATION BY
VIBRATION ANALYSIS, CASE STUDY ECUADOR
ABSTRACT
Exposure to vibrations in
the oil well construction is an inherent phenomenon of drilling operation, the
increasingly complex geometries of the wells, the hardness of the formations
crossed are factors that cause unfavorable conditions and promote a failure of
the drilling tools. The study outlines the optimization process carried out to
drill Napo Formation (Cuenca Oriente) in 12 ¼ “ section using vibration sensors
to record the drilling dynamics; the analysis was performed in three
directional oil wells, the correct interpretation of the records and the
implementation of the recommendations that resulted from the well-to-well
analysis allowed to make changes in the design of the BHA and to establish
parameters of drilling, which result in lower levels of vibration and therefore
in better performances .
Keywords:
Drilling optimization, Drilling problems, Drilling vibrations.
Cita: Ayala, D., Benítez,
A. y Valencia, R. (2017). Optimización de la tasa de penetración mediante el
análisis de las vibraciones al perforar, caso de estudio Ecuador. Revista Fuentes: El reventón
energético, 15 (1), 27-40.
DOI: http://dx.doi.org/10.18273/revfue.v15n1-2017003
1. INTRODUCCIÓN
Una broca que no se adecua correctamente a la formación, los parámetros de
perforación, el BHA, o las herramientas de fondo de pozo, puede introducir
aspectos dinámicos indeseados o generar fuerzas que produzcan la desviación del
pozo respecto de la trayectoria planificada. Por el
contrario, una barrena diseñada correctamente genera un pozo más
calibrado y un trayecto menos tortuoso. (Centale, y otros, 2011)
Los especialistas pueden diseñar una broca que se acople de mejor manera a
la formación y evitar de ese modo las ROP bajas o el tiempo no productivo
excesivo causado por los viajes requeridos para reemplazar las brocas gastadas.
(Ayala, Torres, Valencia y Loaiza, 2016).
La perforación de la sección de 12 ¼”que corresponde a la Formación NAPO
(sucesión de lutitas negras, calizas grises a negras y areniscas calcáreas,
espesor de 200 a 700 metros (Baldock, 1982) , es el intervalo más crítico
durante la perforación, esta sección se la puede dividir en dos intervalos, un
primer intervalo, donde se perfora las formaciones Tiyuyacu y Tena (arcillolita
y entre dos y tres capas de conglomerado, en el caso de Tiyuyacu (Bady,
Rivadeneira, y Barragan, 2004), este intervalo ha sido plenamente optimizado y
no representa ningún problema. En el segundo intervalo se perfora la formación
Napo, al tratarse de una formación intercalada es muy propensa a generar
vibraciones y varios problemas han sido identificados en este intervalo los
cuales son:
·
Daño prematuro de las brocas de perforación. Dos
brocas necesarias para perforar Napo.
·
Alta vibración torsional causando
dificultades para direccionar el pozo.
·
Daño de las herramientas de fondo.
·
Baja ROP debido al desgaste de la estructura de
corte de la broca.
·
Dificultades durante los viajes a
causa de la tortuosidad ocasionada por los problemas direccionales.
·
Varios ensamblajes de fondo y tipos de drive se
probaron para perforar la formación Napo, obteniéndose resultados nada
satisfactorios.
·
Con Motor, los problemas de transferencia de
peso y estoleamiento se traducían en ROP muy bajas (menores a 37 ft/hr), se
observó un daño considerable de la estructura de corte de la broca, con
evidencia de impacto y daño térmico de los cortadores.
·
Utilizando RSS, la vibración
torsional dificultaban considerablemente mantener la dirección del pozo
por los altos niveles de vibración, la broca presenta un desgaste importante
debido a la degradación térmica y daño mecánico, razón por la cual de manera
reiterada se interrumpió la perforación para realizar cambios en el BHA y
broca.
El objetivo de optimizar radica en mejorar el diseño de las brocas, para
reducir el desgaste y el número de brocas utilizadas, la optimización
proporcionará un ahorro en tiempos de viajes y de perforación al incrementar la
ROP. Los antecendetes de otros pozos,
evidencian fuertes niveles vibracionales, por ésta razón, es importante
entenderlas, encontrar sus causas y mitigarlas para conseguir una
perforación eficiente.
1.1. PROBLEMAS ASOCIADOS
A LAS VIBRACIONES
1.1.1 . Rebote de
broca
La acción de corte de las brocas de 3 conos tiende a crear formas lobulares
en el fondo del pozo en formaciones duras, lo que hace que la broca sea
desplazada axialmente 3, 6 o incluso 9 veces por cada
revolución, modificando el peso efectivo sobre la barrena.
Durante este fenómeno, la broca raramente rebota del fondo del pozo, más
bien, se lo debe entender como una fluctuación en el valor de peso
aplicado sobre la broca de forma periódica (DATALOG, 2001).
1.1.2 . “Stick-Slip”
El atascamiento deslizamiento, es un caso severo de vibración torsional,
donde la broca permanece estacionaria por un periodo de tiempo debido a la
fricción producida entre esta y la formación. Cuando el esfuerzo de torsión
dentro de la sarta de perforación es mayor que estas fuerzas de fricción, la
broca se suelta de la pared del pozo y gira por la acción de destornillado de
la columna de perforación genera un movimiento lateral destructivo.
Según los operadoras de perforación, el fenómeno de atascamiento
deslizamiento da cuenta de aproximadamente un 50% del tiempo de perforación en
el fondo del pozo. (Xianping , Páez,
Partin y Agrinhorti, 2010).
Las soluciones más frecuentes usadas en el campo para la reducción del
fenómeno de atascamiento deslizamiento son: el aumento de la velocidad de
rotación, el descenso del WOB o la modificación de las
características de los lodos de perforación. (Sananikone, Kamoshima y
White, 1992)
1.1.3. Remolino
El efecto remolino “whirl”, ocurre cuando hay poco peso sobre la broca o el
número de RPM es muy alto para el tipo de formación geológica. Cuando se
perfora un hoyo en calibre, la broca gira alrededor de su propio centro; pero
durante un movimiento en forma de remolino el centro instantáneo de rotación
pasa a ser un cortador en la cara o el
calibre de la broca, donde uno de los lados de
la broca es empujado contra la pared del pozo por una fuerza centrífuga,
incrementándose la fuerza de fricción y con esto el efecto remolino. (Korin,
et.al., 2015)
Una de las consecuencias del remolino es la generación de un pozo con una
zona de mayor diámetro. Los cortadores se desplazan ocacionando que la broca
recorra distancias más largas por revolución que en un pozo calibrado. Estas
acciones generan cargas de alto impacto sobre la broca y el BHA. (Brelt, Warren
y Behr, 1990).
1.2. REGISTRO DE LA
DINÁMICA DE FONDO
El presente estudio, tendrá como eje principal la medición de vibraciones
torsionales, por ser las más recurrentes durante la perforación con brocas PDC.
El uso de brocas roller cone, será exclusivo para la zona superficial
de los pozos en análisis, por esta razón la cuantificación de las vibraciones
axiales no se llevará a cabo.
En el análisis se empleó tecnología de la compañía NOV Downhole denominada
Black Box, basada en sensores de vibración modo memoria, que se pueden ubicar
estratégicamente en diferentes componentes del ensamblaje de fondo (BHA) para
medir la aceleración lateral y torsional (National Oilwell Varco, 2007).
El registro obtenido con estos sensores, es empatado con la información de
geología, para realizar un análisis completo de la relación entre la dinámica
de fondo y las distintas variables involucradas en la perforación. Fueron
empleados 2 tipos de sensores: Tipo 1 y Tipo 2.
1.2.1 . Tipo 1
Dispositivo de memoria, mide la aceleración de la componente donde fue
situado. Con la señal de aceleración centrípeta se obtiene el valor denominado
Delta RPM, que es el porcentaje de desviación de las RPM de la señal con
respecto a un valor promedio calculado. Con esto se cuantificará
la severidad de la vibración torsional de la que es sujeto un
determinado punto del BHA. (National Oilwell Varco, 2007)
1.2.2 . Tipo 2
Dispositivo de memoria que registra la aceleración tangencial y posición
angular de un determinado punto para
obtener mediante cálculos estadísticos los valores de RMS, impactos laterales, Delta RPM y RPM de
fondo. La ventaja que tiene sobre el sensor tipo 1, es que arroja las RPM que se tienen en fondo con mayor
precisión, representando de mejor manera el rango dinámico Delta RPM. (National
Oilwell Varco, 2007).
1.3. ANÁLISIS DE LA
DINÁMICA DE FONDO
1.3.1 . Coca K -29
Pozo direccional tipo “J”, con una inclinación máxima planeada de 28°. Para perforar la formación Napo se utilizó
el BHA descrito en la tabla 1, y la conficuración de los sensores
detallado en la tabla 2.
Tabla 1. BHA Coca K-29
|
Información
BHA
|
BHA
|
Direccional
|
Sistema
direccional
|
RSS
|
Broca
|
PDC 5 aletas
|
Cortadores
|
19 mm
|
Tabla 2. Sensores Coca K-29
|
Configuración de
Sensores
|
|
Sensor
|
Ubicación
|
#
Sensores
|
Tipo 2
|
Interior broca
|
1
|
Tipo 1 Sobre monel 2
Tipo2
|
Entre HWDP a 558 ft de la
broca
|
2
|
El BHA ingresó a 8412 ft y avanzó hasta 9140 ft, después de
perforar 728 ft el BHA fue sacado a superficie por tener una baja ROP.
La valoración del estado de la broca se indica en la tabla 3.
Tabla
3. Estado de la Broca
Diagnóstico de la Broca
Desgaste
considerable por impacto y degradación térmica
Código IADC del desgaste de la broca
0-4- WT-S-X-1-CT/HC-PR
El registro de vibraciones de la
figura 1, muestra que se perforó bajo vibración torsional severa en
la broca y BHA con acoplamiento de vibración lateral.
|
|
·
Vibración torsional en la broca (sensor de
la broca) superior al 90%, vibración torsional en el BHA ( sensor sobre el
monel) superior al 50%.
·
Incremento de vibración torsional al
perforar caliza y arenisca.
·
Vibración lateral en la broca alrededor de
0.8 (g), y la vibración lateral en el BHA alrededor de 1.8 (g).
·
Acoplamiento de la vibración lateral con la
vibración torsional.
|
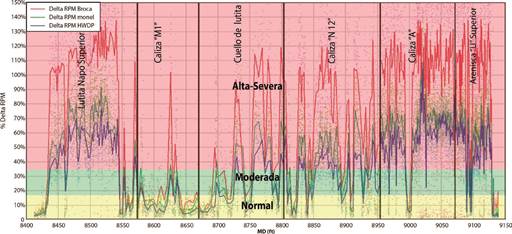
Figura 1. Vibración
torsional en MD, Coca K 29.
|
La intensidad de la vibración torsional indica que la propagación va en el
sentido de la broca hacia arriba, en el BHA y en el HWDP, y de acuerdo al
comportamiento dependiente de la litología, es evidente que la vibración
torsional se está originando de la interacción entre la broca y la
formación, la figura 2, muestra que hay una relación entre los
parámetros y la vibración torsional.
•
Incremento de la vibración torsional conforme
incrementa el WOB.
•
Reducción de la vibración torsional conforme
incrementa las RPM.
•
La vibración lateral así como la vibración
torsional muestran una misma relación con respecto a los parámetros de
perforación.
Con la figura 2, se puede establecer los valores óptimos de
WOB y RPM para perforar esta formación y son: WOB menor a 4 klb o RPM mayor a
225 RPM.
Con estas medidas se optimizará el proceso y se reducirán los niveles de
vibración torsional, especialmente en la broca.
El WOB que normalmente se requiere para vencer la compresibilidad de la
formación, es mucho mayor al necesario para tener vibraciones de intensidad
baja. La opción de controlar la vibración torsional por WOB queda descartada;
la otra alternativa es incrementar las RPM en la broca por arriba de 200 RPM,
esto provee mayor energía a la broca, lo que permite vencer la resistencia de
la roca evitando que se detenga la rotación.
Por lo amprendido en el pozo Coca K-29, se implementaran los siguientes
cambios en el BHA para el nuevo pozo:
•
Cambio de RSS por Motor de Fondo con una salida
de torque de media a alta (lobe 7:8, 4 etapas).
•
Inclusión de la herramienta de oscilación axial.
La inclusión de la herramienta de oscilación axial se lo hace para reducir
la fricción de la sarta de perforación
con las paredes del hoyo, que genera problemas de arrastre, baja ROP deslizando
y problemas de estoleamiento de motor.
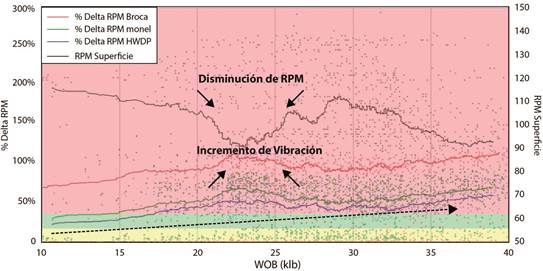
Figura
2. Vibración torsional Vs WOB y RPM de superficie en la Lutita.
|
|
Pozo direccional tipo “J” con una inclinación máxima planeada de 29.88°.
Para perforar la formación Napo se utilizó un BHA fulcro descrito en la tabla
4, y la configuración de los sensores en la tabla 5.
Tabla 4. BHA Coca K-40
|
Información
BHA
|
BHA
|
Direccional
|
Sistema
direccional
|
Motor de fondo
|
Broca
|
PDC 5 aletas
|
Cortadores
|
19 mm
|
Tabla 5. Sensores Coca K-40
|
Configuración
de Sensores
|
|
Sensor
|
Ubicación
|
#
Sensores
|
Tipo 2
|
Interior broca
|
1
|
Tipo 1 Sobre monel 2
Tipo2
|
Arriba del estabilizador, 1257 ft sobre la broca
|
2
|
En este caso, el BHA perforó unos pocos pies de Tena antes de ingresar a
Napo, y adicionalmente por necesidad de toma de coring la perforación fue
interrumpida, perforando únicamente 681 ft, de los cuales 616 ft fueron de
Napo.
La figura 3, muestra el registro de vibraciones donde se
puede ver que la vibración torsional es mayor en la broca. Mostrando el
siguiente comportamiento:
•
Vibración torsional en la broca (sensor ubicado
en la broca) alrededor de 41% y en el BHA (sensor ubicado en el monel)
alrededor de 19%.
•
Vibración lateral en la broca alrededor de 0.43
(g) y en el BHA alrededor de 0.19 (g), no representa ningún problema.
Comparado con el pozo anterior, los niveles de vibración son mucho menores.
La vibración torsional en la broca se redujo en 54%, la vibración torsional en
el BHA se redujo en 62%. La vibración Lateral en la broca se redujo en 43% y la
vibración lateral en el BHA se redujo en 89%. Esto se tradujo en un incremento
de la ROP neta en un 95%.
El desgaste de la broca fue significativamente menor y la
valoración del estado de la herramienta se indica en la tabla 6.
Tabla 6. Estado de la Broca.
Desgaste moderado por impacto y degradación térmica
Código IADC del desgaste de la broca
0-1- WT-S-X-1-NO-BHA
El pozo Coca K-40 estableció los parámetros óptimos para perforar la
formación Napo, con un ensamblaje de motor que permite mitigar las vibración
torsional y lateral así como obtener mayor ROP.
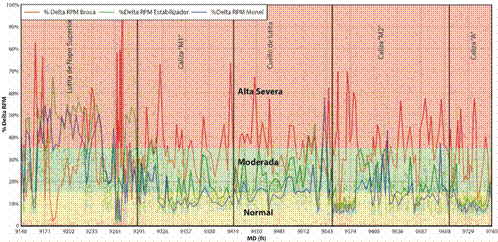
Figura 3. Vibración
torsional en MD Coca K-40
|
1.3.4. CoCa K-41
Es un pozo direccional tipo “J” de 40.3° de inclinación máxima. El objetivo
direccional en la formación Napo es mantener tangente en 30°. El BHA utilizado
es similar al pozo Coca K-40 y se lo detalla en la tabla 7, y
la configuración de los sensores en la tabla 8.
Tabla 7. BHA Coca K-41
Información BHA
|
BHA Direccional
|
Sistema direccional Motor de fondo
Broca
|
PDC 5 aletas
|
Cortadores
|
19 mm
|
Tabla
8. Sensores Coca K-41.
|
Configuración de
Sensores
|
|
Sensor
|
Ubicación
|
# Sensores
|
Tipo 1
|
Interior broca
|
1
|
Tipo 1 Sobre monel 2
Tipo2
|
Arriba de estabilizador,
1245 ft Sobre la broca
|
2
|
El BHA ingresó a 9717 ft y salió a 10964 ft. Perforando 1247 ft de la
formación Napo e ingresando unos pocos pies en la formación Hollín (arenisca
cuarzosa de grano fino,con contenido alto o medio de
glauconita (Bady, Rivadeneira y Barragan, 2004). La figura 4, muestra el registro de vibraciones
para toda la corrida. Se observa que los niveles de vibración torsional son muy
bajos y por lo tanto aceptables.
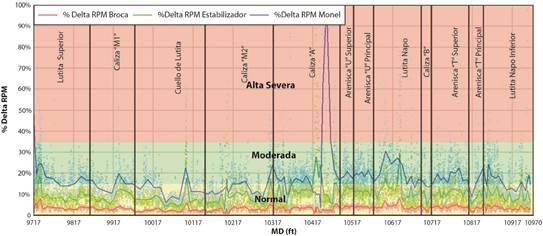
Figura 4. Vibración torsional en MD Coca K-41
|
•
Vibración Torsional en la Broca alrededor de 4%
y en el BHA alrededor de 18%.
Este resultado se obtuvo al aplicar los parámetros de perforación (RPM y
WOB) obtenidos del pozo Coca K-40.
Para esta corrida, se registra un ligero incremento en la vibración
lateral, lo cual era de esperarse por los parámetros recomendados, sin embargo
los niveles de esta vibración se mantienen en niveles muy bajos.
La vibración torsional en la broca se redujo en 90% y en
el BHA en 5%. Lo que se refleja en el desgaste de la broca, la
valoración del estado de la barrena se indica en la tabla 9.
Tabla 9. Estado de la Broca.
Desgaste moderado por impacto y degradación térmica
Código IADC del desgaste de la broca
0-1- WT-S-X-1-CT-TD
2 . RESULTADOS
El estudio consideró las recomendaciones de los investigadores de Smith.
El análisis de los datos se lo debe
realizar en un ambiente de perforación virtual junto con la información
relacionada con la broca específica a evaluar, la evaluación debe incluir:
Localización precisa, propiedades del material y dimensiones de los
cortadores.
Datos dimensionales de los componentes de fondo de pozo y las
características físicas de cada elemento del BHA.
Geometría del pozo propuesto.
Parámetros operativos planificados (Garret, Teggart y Tetley, 2010).
El análisis incorpora la variación de las vibraciones para la broca y BHA
según la profundidad en TVD para los 3 pozos de estudio Coca K-29, Coca K-40 y
Coca K-41, donde se puede apreciar la variación de la vibración en los 3 pozos
de acuerdo a la litología atravesada.
2.1. VIBRACIÓN TORSIONAL EN LA BROCA
La figura 5, recopilados los datos de la vibración torsional que afectó a la
broca en profundidad TVD y por sub-formación.

Figura 5. Vibración torsional en la broca según
subformaciones.
De la figura 5 se destaca lo siguiente:
•
El último pozo perforado Coca K-41, presenta los
menores niveles de vibración torsional en la broca y el pozo Coca K-29 es el
que registra los niveles más altos de vibración torsional.
•
Reducción significante de 51% de
vibración torsional en la broca para el pozo Coca K-40 y del 96% en el
pozo Coca K-41 respecto al pozo inicial Coca K-29.
•
Vibración torsional en la broca de nivel normal
únicamente en el pozo Coca K-41, lo que permitió un uso eficiente de la energía
suministrada a la broca optimizando la perforación.
•
Vibración torsional al perforar la caliza “M1”,
es mayor en el pozo Coca K-40, debido al efecto de resonancia presente en la
mayor parte de esta subformación.
•
De los paquetes de caliza que conforman Napo, la
caliza “A” es la que muestra la mayor intensidad de vibración torsional.
2.2. VIBRACIÓN TORSIONAL
EN EL BHA
En la figura 6, se presenta la gráfica como resultado de
haber tabulado los datos de la vibración torsional que afectó al BHA en
profundidad TVD y por subformación:
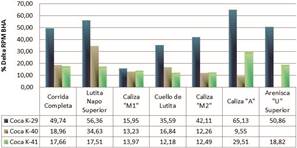
Figura 6. Vibración torsional en el BHA por
subformaciones.
Del análisis de los datos de figura 6 se obtuvo:
•
Los pozos Coca K-40 y Coca K-41 presentan
niveles normales de vibración torsional en el BHA.
•
Niveles de vibración torsional en el BHA
similares en el pozo Coca K-40 y Coca K-41, siendo el Coca K-41 el que menores
niveles registró.
•
Reducción del 62% de la vibración torsional en
el pozo Coca K-40 y del 65% en el Coca K-41.
•
Aumento de la actividad torsional en la caliza
“A” y la arenisca “U” superior.
•
De los paquetes de caliza que conforman Napo, la
caliza “A” es la que muestra un mayor nivel de vibraciones torsionales.
2.3. EVALUACIÓN DE ROP
La figura 7, muestra el incremento de ROP, de 23 ft/h en
el pozo Coca K-29 a 45 ft/h en el pozo Coca K-40 y llegó a 48 ft/h en Coca
K-41, es decir, un incremento del 109 % de la ROP comparado con el pozo
inicial.
El pozo Coca K-41, que muestra el mayor desempeño, estuvo sometido a
ciertas condiciones que deben ser consideradas:
•
ROP instantánea limitada a 70 ft/h. Esto no
permite evaluar cuál es el desempeño que puede alcanzar la broca perforando
Napo.
•
Mayor inclinación (40.3º) y mayor desplazamiento
horizontal que los pozos anteriores.
•
Mayor intervalo perforado de Napo, llegando a
atravesar toda esta formación, son 500 ft más que se perforaron respecto a los
pozos que le anteceden.
•
Mayor intervalo deslizado: 43 ft en Coca K-41 y
17 ft en Coca K-40.
Se logró un incremento de la ROP, muestra de que la dinámica del BHA fue
optimizada exitosamente.
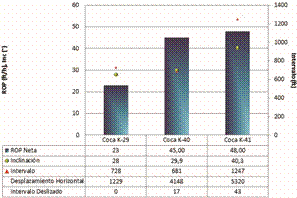
Figura 7. Comparación desempeños Coca K-29, Coca
K-40 y Coca K-41.
2.4. CONDICIÓN DE DESGASTE
Se analiza la broca para determinar el desgaste y la rotura de la
estructura de corte. La industria establece directrices generales para
relacionar los patrones de desgaste habituales de las brocas con las posibles
causas ( Betson y Smith, 1956).
El desgaste de las brocas corridas para perforar Napo en los pozos de estudio,
según el código IADC (García, 2008) son
los siguientes :
•
Coca
K-29 con 0-4-WT-S-X-1-CT/HC-PR
•
Coca
K-40 con 0-1-WT-S-X-I-NO-BHA.
•
Coca
K-41 con 0-1-WT-S-X-1-CT-TD.
El desgaste mínimo y la buena condición de la broca contribuyeron para
lograr una ROP más alta y alcanzar una mejor dinámica de fondo, lo que permitió
hacer uso de una sola broca para atravesar toda la formación Napo,
eliminando viajes no planificados por cambio de broca.
2.5. LINEAMIENTOS PARA LA CONFIGURACIÓN DEL BHA
El proceso iterativo para el desarrollo de configuraciones óptimas de brocas y
BHA también es obstaculizado por diversos factores inherentes al
proceso. Los ingenieros con distintas experiencias extraen conclusiones
disímiles a partir de patrones de desgaste esencialmente iguales; por ejemplo, algunos
ingenieros pueden identificar la causa de un determinado patrón de
desgaste luego de formular supuestos falsos. El más común de estos supuestos es
que el peso de la sarta de perforación es transferido a la broca
de manera eficiente. El WOB incide directamente en la ROP. Un ingeniero
puede asumir que la selección deficiente de la broca está dificultando
la ROP cuando en realidad el WOB, que es una función del diseño del BHA,
es en efecto inferior al valor calculado. Por el contrario, cuando , el WOB es
demasiado alto, la sarta de perforación y el BHA pueden flexionarse, lo que genera un
pozo de mayor diámetro y produce vibraciones laterales destructivas ya
que la broca angular se acciona y corta la pared del pozo. (Wiliamson y Lumbiski,
1986).
El plan direccional en Napo requiere mantener la tangente hasta la lutita
de Napo Intermedia (lutitas laminadas negras (Salazar y Sáchez, 1989), e
iniciar la caída de ángulo hasta llegar a TD al tope de Hollín. Para cumplir
este objetivo, es necesario emplear un BHA tipo fulcro que permita contener la
caída natural del ángulo generado en las lutitas de Napo, consideración que ya
ha sido ampliamente estudiada por la compañía direccional y no forma parte de
este estudio.
Los objetivos direccionales han sido alcanzados con éxito durante las
operaciones de los pozos Coca K-40 y Coca K-41 llegando a cumplir el programa
planteado. Se debe enfatizar que los lineamientos sobre la
configuración de BHA que se detallarán, están orientados al correcto
funcionamiento de la dinámica de fondo más que al cumplimiento del plan
direccional. Estos lineamientos deben ser aplicados a pozos direccionales tipo
“J” que tengan ángulos de inclinación similares a los pozos de estudio, es
decir entre 30° y 40°.
Las siguientes consideraciones fueron adoptadas en los pozos Coca K-40 y
Coca K-41 en base del análisis de vibraciones realizado:
•
Empleo de un motor con alto torque de salida.
Esto con el fin de entregar mayor potencia en fondo para
vencer el torque generado por la interacción broca-formación. En Ecuador el tipo de motor que se encuentra
disponible tiene relación de lóbulos 7/8 con 4 etapas, lo cual cumple con este
requerimiento.
•
La configuración de tamaños de los
estabilizadores debe ser de 12 inch en la camisa estabilizadora del
motor y de 11.75 inch en el estabilizador que ha sido ubicado sobre el motor
(García, 2008).
•
Los ángulos de inclinación de los pozos están entre
los 30° y 40° por lo que la configuración de estabilizadores se mantuvo
en estos 2 pozos (Coca K-40 y Coca K-41), sin embargo, la dinámica de fondo
puede cambiar si la disposición de estabilizadores se modifica en orden
de alcanzar otro tipo de objetivos direccionales. La aplicación de
los lineamientos se limita a pozos con perfiles direccionales en el
rango ya establecido.
•
Empleo de una broca de 5 aletas con cortadores
de 19 mm y componentes secundarios controladores de torque, estos elementos son
importantes, porque minimizan el riesgo de vibración torsional por penetración
exagerada de los cortadores en la formación.
•
Aplicación de tecnología reductora de fricción
(tubería-paredes del hoyo), para mejorar así la transferencia de peso hacia la
broca, obtener un torque más estable y con esto reducir los niveles de
vibración torsional (Schlumberger). Se emplearon herramientas reductoras en los
pozos Coca K-40 y Coca K-41.
•
Para el caso específico de esta
herramienta el caudal óptimo de trabajo oscila entre 600 gal/min y 900
gal/min, con una caída de presión que varía entre 200 y 400 psi.
•
El posicionamiento del reductor de fricción,
debe ser por lo menos 1200 ft sobre la broca para que la frecuencia de trabajo
de la herramienta no afecte a la del MWD. Dicha frecuencia está entre 14.9-18.0
Hz, por tal razón, se debe configurar la frecuencia
del MWD lo más baja posible.
•
La ubicación exacta de la herramienta será
determinada mediante simulación.
•
Con el caudal óptimo de trabajo, 800 psi y
densidad del lodo de 11.5 lb/gal, la caída de presión que genera la herramienta
es 350 psi y frecuencia de trabajo de 16
Hz.
La tabla 10, presenta un ejemplo de BHA que cumple con
los requerimientos establecidos anteriormente.
Tabla 10. Configuración de BHA Coca K-41.
OD Max
Longitud
(in) OD Longitud
N° Descripción acumulada

( ft )
ID (in) (in) (ft)
|
12 1/4” PDC Bit E1134 8
1 12.25 1.17 1.17
- IADC M423 3.25
|
Motor lóbulos 7/8, 4 8.25
3 etapas / Factor 0.16, BH 12 29.72 31.89
1.5°, 12 in Estabilizador 6.25
5
|
Estabilizador
|
8.25
2.84
|
11.75
|
7.25
|
43.14
|
6
|
LWD
|
8.38
3
|
9.13
|
19.4
|
62.54
|
7
|
MWD
|
8.25
5.9
|
8.38
|
27.35
|
89.89
|
8
|
Monel
|
8.25
2.81
|
9.1
|
21.19
|
111.08
|
10
|
X-O (2 juntas)
|
9.5
3.38
|
9.5
|
2.63
|
117.71
|
11
|
HWDP (33 juntas)
|
5
3
|
6.5
|
1003.22
|
1120.93
|
12
|
Martillo Hidráulico
|
6.5
2.75
|
6.5
|
31.55
|
1152.48
|
13
|
HWDP (3 juntas)
|
5
3
|
6.5
|
92.41
|
1244.89
|
14
|
Herramienta reductora de fricción
|
6.75
2.25
|
6.75
|
26.53
|
1271.45
|
16
|
HWDP
|
5
3
|
6.5
|
30.61
|
1302.06
|
17
|
Intensificador
|
6.5
2.75
|
6.5
|
32
|
1334.06
|
18
|
HWDP (3 juntas)
|
5
3
|
6.5
|
91.32
|
1425.38
|
19
|
X-O
|
6.5
2.81
|
6.5
|
2.67
|
1428.05
|
Se debe tomar en cuenta lo indicado por Cassaneli JP, Franco M. Pérez LC,
Pinheiro C y Frenzel M en el momento de programar futuras operaciones de
optimización, porque, el enfoque de tipo prueba y error respecto de los cambios
del BHA permitían aliviar levemente las vibraciones axiales y laterales, pero
exacerban la severidad del fenómeno de atascamiento deslizamiento. (Cassaneli,
Franco, Pérez, Pinheiro y Frenzel, 2008).
2.6 . DEFINICIÓN DE PARÁMETROS
En el paper Improving Drilling Performance by Applying Advanced Dynamics
Models, se indica que los sensores de fondo de pozo y de
superficie monitorean las vibraciones relacionadas con disfunciones.
Sobre la base de las mediciones obtenidas con los sensores, los resultados de
los modelos y la experiencia previa en operaciones de perforación en el campo.
Los ingenieros ajustan los parámetros para optimizar la ROP y minimizar las
vibraciones destructivas. (Dykstra, Neubert, Hanson y Meiners, 2001), se
incorporará esta recomendación en los tres pozos estudiados.
En base al análisis obtenido del registro de vibraciones de los pozos (Coca
K-29, Coca K-40, Coca K-41), en conjunto con la evaluación de la efectividad de
las medidas preliminares adoptadas, se determinará el mapa de parámetros que
mejor se adapte para perforar las subformaciones de Napo (sección 12 ¼ “) del
Campo Coca.
2.6.1. Determinación de RPM y WOB en la caliza “A” de la
formación Napo
Mediante gráficas de contorno se mostrará la dependencia
entre ROP, WOB y RPM en superficie para cada una de las sub-formaciones
de Napo. Las zonas rojas representan la combinación de parámetros que generan
mayor vibración.
Debido a la extensión del análisis y la gran cantidad de gráficas
generadas, se detallará únicamente el proceso para obtener las RPM y WOB
óptimos para perforar la caliza “A” (calizas micríticasmasivas y laminadas, con
abundante cherts negros, presenta silicificación y abundante pirita
(Jaillard, y otros, 2007)). Para realizar un análisis más exhaustivo sobre el
comportamiento de las vibraciones, se dividió las sub-formaciones de Napo de
acuerdo a la litología que contienen, como se0 aprecia en la columna 2 de la
tabla 3.
En las gráficas de contorno, se muestra la relación de las vibraciones en
la broca y BHA con las RPM de superficie y WOB aplicados para perforar la
lutita y caliza que conforman la caliza “A”.
Los valores de vibración torsional identificados son los típicos, sin embargo se trata
de trabajar en zonas donde la vibración sea la menor posible. Se puede observar
que con RPM entre 72-85 y WOB entre 15 y 40 klb se tiene la menor vibración
torsional en la broca dentro de la caliza. Ver figura 8.
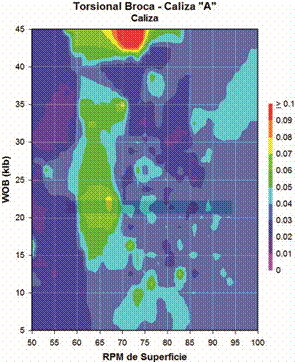
Figura 8. Vibración torsional broca caliza-caliza
“A”.
Al analizar la lutita que contiene la caliza “A”, se observa que
con RPM de superficie entre 70-85 y WOB mayor a 25 klb se generaron
niveles más bajos de vibración torsional en la broca. Ver figura 9.
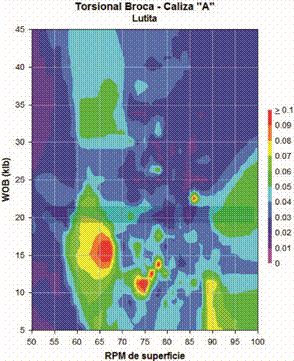
Figura 9. Vibración torsional broca lutita-caliza
“A”.
Para el BHA, a bajas RPM, la vibración torsional es alta a cualquier valor
de WOB en la caliza y los niveles más bajos de vibraciones, se obtiene al
superar las 70 RPM y WOB entre 24-35 klb. Ver figura 10.
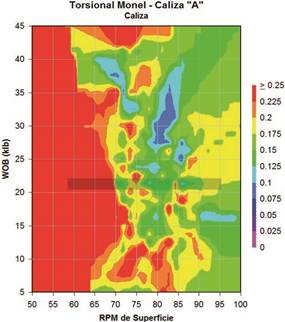
Figura 10. Vibración torsional monel caliza-caliza
“A”.
En los paquetes de lutita de la caliza “A”, se mantiene la tendencia de
altos niveles de vibración con bajas RPM a cualquier valor de WOB. Para trabajar con una vibración torsional
leve, se debería aplicar más de 70 RPM y el WOB debería variar entre 25-35 klb.
Ver figura 11.
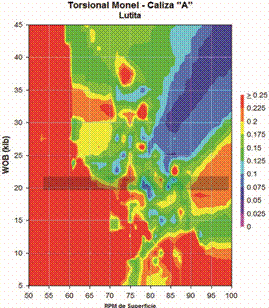
Figura 11. Vibración torsional monel lutita-Caliza
“A”.
Además, al observar la relación del desempeño con los parámetros aplicados,
considerando que las RPM oscilan entre
65 y 77, en conjunto con WOB mayor a 30, se obtienen las más altas tasas de
penetración en los paquetes de caliza. Ver figura 12.
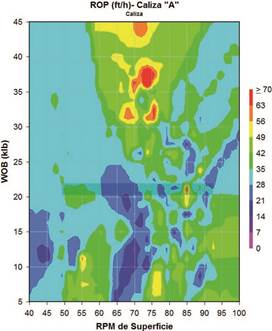
Figura 12. ROP caliza-caliza “A”.
En los paquetes de lutita se obtiene las tasas de penetración más altas,
con valores de RPM entre 60 y 77 y variaciones de WOB mayores a 32 klb. Ver figura 13.
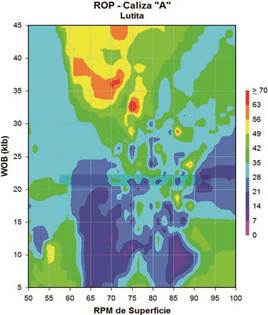
Figura 13. ROP caliza-caliza “A”.
2.6.2. Parámetros para perforar la formación Napo
El procedimiento realizado para encontrar las RPM y el WOB óptimos para
peforar la caliza “A” (descrita en la tabla 11) fue el utilizado para detallar
los parámetros del resto de sub-formaciones de Napo.
Finalmente, con los parámetros establecidos para la broca y BHA según la
litología de la subformación Napo, se realizó una intersección de los
parámetros en común que generen menor vibración torsional y lateral de la mano
con un alto desempeño.
La tabla 12, presenta el mapa de parámetros final, los cuales
al implementarse podrían presentar pequeños intervalos en los que por diversas
situaciones operacionales se puedan modificar.
Tabla 12. Mapa de parámetros para perforar Napo.
Sub-Formación
|
Litología
|
WOB
|
RPM
|
|
|
|
|
|
Min
|
Max
|
Min Max
|
Lutita Napo Superior
|
Lutita
|
25 37
|
75 80
|
|
Caliza
|
25 37
|
75 80
|
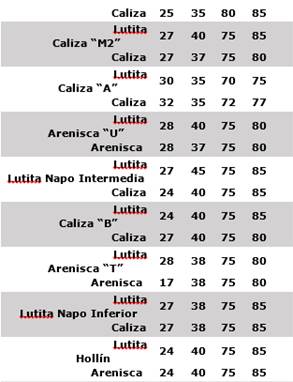
Lutita 28 38 75 85
2.6.3. Caudal para
perforar la formación Napo
La caliza por su dureza tiende a generar vibración torsional de mayor
intensidad como se ha demostrado en este estudio, esto se debe a que requiere
de una gran cantidad de energía para vencer su resistencia. Esta energía
se suministra desde superficie en forma de RPM o caudal para el caso de
un motor de fondo, por lo tanto, si se considera el factor vibración, un alto
caudal es de gran ventaja, puesto que entregaría más RPM en fondo y se
dispondría de suficiente energía para vencer el torque reactivo de esta
litología y así reducir la intensidad de la vibración torsional.
Son varias las ventajas de manejar un alto caudal, sin embargo, existen
limitantes al valor máximo que se puede emplear.
•
Los rangos de trabajo que manejan las
herramientas direccionales para su correcto funcionamiento. Para el caso de un
motor con una salida de torque como el utilizando en este análisis, relación de
lóbulos 7/8, 4 etapas, bent housing 1.5° y factor 0.16, se maneja un rango
entre 400 gpm y 880 gpm.
•
Las pérdidas de presión por fricción generadas
al conducir el fluido de perforación hacia el fondo del pozo
a través de la tubería. La presión de superficie máxima con la que
trabaja el taladro de perforación generalmente es de 3800 psi.
Realizar los cálculos hidráulicos es fundamental porque permiten conocer la
presión que se esperaría tener con el BHA, considerando las caídas de presión
por herramientas direccionales, MWD, LWD, Motor, la caída de presión de la
herramienta de oscilación axial y el diferencial aplicado con el motor a la
hora de perforar.
Los cálculos de hidráulica para perforar Napo a la profundidad de salida de
la corrida 10964 ft, con el tipo de BHA empleado en el pozo Coca K-41 con 4 se
los realizó valores de caudal y los resultados se presentan en la tabla 13, que
resume la hidráulica.
El valor máximo de caudal que cumple con los requerimientos direccionales,
no excede la presión de las bombas del taladro y permitirá obtener las ventajas
ya expuestas es 800 gal/min. Estos cálculos consideraron un peso de lodo de
11.5 lb/gal, viscosidad plástica 22 cp y un punto cedente 26 lb/100 ft2 que
generalemte se utilizan para perforar Napo. La broca fue configurada con
7 boquillas de 16/32 de pulgada, obteniéndose un TFA de 1.374 in2.
Tabla 13. Cálculos de Hidráulica.
Tasa de Flujo ( gal/min )
|
780
|
790
|
800
|
810 820
|
Presión de Superficie
(psi)
|
3651
|
3712
|
3774
|
3837 3900
|
Equipo Superficie ( psi )
|
13.7
|
13.8
|
13.9
|
14 14.1
|
Flujo de Broca ( gal/min )
|
757
|
766
|
776
|
786 795
|
Caída de Presión de Broca (psi)
|
321
|
329
|
338
|
346 355
|
HP/ HSI Broca
|
142/120
|
147/1.25
|
153/1.3
|
159/1.35
165/1.4
|
Velocidad Chorro
( ft/s )
|
177
|
179
|
181
|
183 186
|
2.6.4. Problemas de control asociados
Los problemas de control asociados a la dinámica presentada de la sarta de
perforación son los siguientes:
•
Mantenimeinto de la velocidad del mecanismo rotario
de la superficie constante.
•
Reducción de las oscilaciones de
atascamientodeslizamiento.
•
Mantenimiento de condiciones óptimas de
operación. (Navarro y Suárez, 2004)
La propuesta descrita en el Mapa de Parámetros para Perforar Napo (tabla
12), permite direccionar las soluciones bajo un esquema de control de
parámetros de perforación y diseño de BHA.
3. CONCLUSIONES
•
Se demostró que es posible atravesar toda la
formación Napo con una sola broca y en una sola corrida.
•
Las intercalaciones de caliza y arenisca de la
formación Napo, representan un mayor potencial de generación de vibraciones
debido a la alta compresibilidad que poseen. Mayores niveles de vibración
torsional y lateral son registrados cuando se emplea un sistema rotatorio dirigible
RSS, puesto que, no entrega la suficiente cantidad de energía a la
broca para vencer el torque reactivo de la litología de Napo.
•
El incremento de las RPM de fondo entregado por un
motor, reducen significativamente los niveles de vibración torsional en
la broca y vibración lateral en el BHA al tener que aplicarse menor cantidad de
RPM en superficie, así queda demostrado que utilizar motor de fondo es un
método eficiente para resolver los problemas de vibración torsional
originados en la interacción broca-formación.
•
La adaptación continua de parámetros de
perforación RPM y WOB permitió obtener una dinámica de fondo más equilibrada en
conjunto con la mayor ROP en el último pozo de estudio, Coca K-41:
•
Se logró reducir en un 51% los niveles de
vibración torsional en la broca para el pozo Coca K-40 y del 96% en Coca K-41
en los cuales se empleó motor respecto a Coca K-29 donde se utilizó un RSS.
•
Se incrementó la ROP que pasó de 23 ft/h en el
pozo Coca K-29 a 45 ft/h en Coca K-40 y a 48 ft/h en Coca K-41, es decir, un
incremento del 109% de la ROP comparado con el pozo inicial.
4. BIBLIOGRAFÍA
1.
Ayala, D., Torres, F., Valencia, R. y Loaiza, M.
(2016). Impacto del Tiempo no Productivo en Operaciones de Perforación y
Análisis de los datos Mediante la Prueba de Chicuadrado. Fuentes El Reventón Energético, 11.
2.
Baldock.
J. (1982). Geology of Ecuador. (pág. 20). Quito: Dirección General de
Geología y Minas.
3.
Bady. P., Rivadeneira. M. y Barragán. R. (2004).
La Cuenca Oriente: Geología y
Petróleo. Quito: Editores Científicos.
4.
Betson,
H. y Smith, H. (1956). Rock-Bit Desing, Selection and Evaluation. API 56-288, 35.
5.
Brelt,
J., Warren, T. yBehr, S. (1990). Bit Whirl –A new Theory of PDC Bit Failure. SPE 19571-PA, 275.
6.
Cassanelli, J., Franco, M., Pérez, L., Pinheiro,
C. y Frenfel, M. (2008). Dynamic Simulation Solving
Vibration/Stick-Slip Issues Achieves Record ROP, Pagoreni Field. Perú. Lima.
7.
Centale, P., Chala, V., Meehan, R., Páez, L.,
Partin, U., Segal, S., Wu, S., Garret, I., Teggart, B., Tetley, B. (2011). El
diseño de las barrenas: Desde arriba hasta abajo. Sugar Land: Oilfield Review, 17
8.
DATALOG. (2001). Datalog Manual de Operaciones en el Pozo
(Tercera ed.).
9.
Dykstra, M., Neubert, M., Hanson, J. y Meiners,
10.
M.
(Marzo de
2001). Improving Drilling Performance by Applying Advanced Dynamics Models. SPE/IADC
67697-MS, 18.
11.
Garret.
I., Teggart. B. y Tetley. (2010). FEA Modeling system Delivers High-Angle
Well Bore through Hard Formations. E&P 83, no. 9.
12.
García,
R. (2008). Estudio del Rendimiento de la broca HCM605Z para la sección de 12
1/4” diseñada para la perforación de pozos horizontales en el campo Tarapoha.
Guayaquil: Escuela Politécnica del Litoral.
13.
Jaillard, E., Benqston, P., Ordoñez, M., Vaca.
W., Dhondt, A., Suárez, J., Toro, J. (2007). Sedimentary
record of terminal Cretaceous accretions in Ecuador. Journal of South America
Earth Sciences.
14.
Korin, I., Morris, W., Gómez, M., Achem, H.,
Rodriguez, J. y Oroña, J. (2015).
Desarrollo e Implementación de un Sensor de Vibraciones. San
Antonio.
15.
Navarro, E. y Suárez R. (2004). Vibraciones en una Sarta de
Perforación: Problemas de Control. ( pág. 6). Mexico: CONACYT
35989-A.
16.
National
Oilwell Varco. (2007). A Guide to Drilling Vibration.
Houston.
17.
Salazar, F. y Sánchez, H. (1989). Evaluación de las Arcillas en la
Formación Napo, Areniscas «U» y «T» en la Cuenca Oriente. (pág.
158). Quito: Universidad Central del Ecuador.
18.
Sananikone, P., Kamoshima, O. y White, D.
(1992). A Field Method for
Controlling Drillstring
19.
Torsional
Vibrations. Proceedings of the IADC/ SPE Drilling Conference (págs. 443-452). IADC/SPE
23891.
20.
Schlumberger.
(s.f.). Sensores y Optimización de la Perforación. ( pág. 16).
21.
Williamson,
J. y Lumbiski, A. (1986). Predicting Bottom hole Assembly Performance. IADC/ SPE 14764-PA, 13.
22.
20.Xianping,
S., Páez, J., Partin, U. y Agrinhorti, M. (2010). Decoupling Stick-Slip and
Whirl to Achieve Breakthrough in Drilling Performance. IADC/SPE 128767-MS, 13.